塑件的外部和內(nèi)部形狀是由型腔和型芯直接成型的,這些復(fù)雜的立體型面加工難度比較大,特別是型腔的盲孔型內(nèi)成型表面加工,如果采用傳統(tǒng)的加工方法,不僅要求工人技術(shù)水平高、輔助工夾具多、刀具多,而且加工的周期長。
The external and internal shapes of plastic parts are directly formed by the cavity and core. It is difficult to process these complex three-dimensional surfaces, especially the blind hole internal forming surface of the cavity. If the traditional processing method is adopted, it requires not only high technical level of workers, many auxiliary tools and tools, but also a long processing cycle.
激光盤記錄面的粗糙度要達(dá)到鏡面加工的水平的0.02-0.01μm這就要求山東模具制造廠家的模具的表面粗糙度達(dá)到0.01μm以下。長壽命注塑模具對于提高率和降低成本是很必要的,目前注塑模具的使用壽命一般要求100萬次以上。
The roughness of the recording surface of the laser disk shall reach 0.02-0.01 of the level of mirror machining μ M this requires that the surface roughness of molds manufactured by Shandong mold manufacturers reach 0.01 μ M or less. Long life injection mold is necessary to improve efficiency and reduce cost. At present, the service life of injection mold generally requires more than 1million times.
精密注塑模要用剛度大的模架,增加模板的厚度,增加支承柱或錐形定位元件以防止模具受壓力后產(chǎn)生變形,有時(shí)內(nèi)壓可以達(dá)到100MPa。
The precision injection mold should use the mold base with high rigidity, increase the thickness of the template, and increase the support column or conical positioning element to prevent the deformation of the mold under pressure. Sometimes the internal pressure can reach 100MPa.
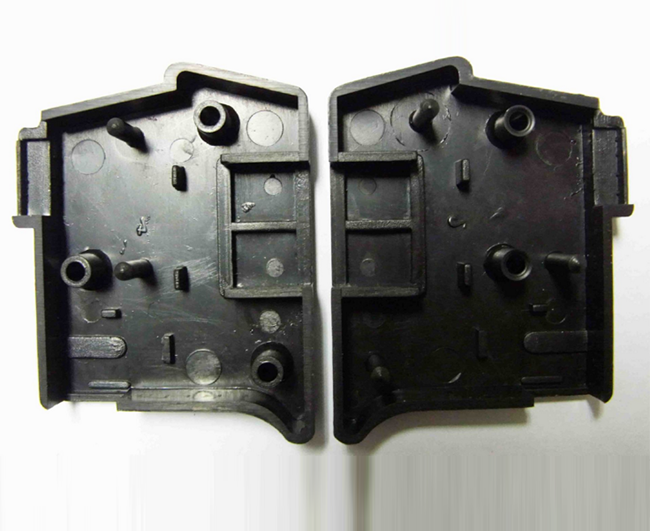
頂出裝置是影響制品變形和尺寸精度的重要因素,因此應(yīng)該選擇佳的頂出點(diǎn),以使各處脫模均勻。高精度注塑模具在結(jié)構(gòu)上多數(shù)采用鑲拼或全拼結(jié)構(gòu),這要求模具零部件的加工精度、互換性均大為提高。
Ejection device is an important factor affecting product deformation and dimensional accuracy. Therefore, a good ejection point should be selected to ensure uniform demoulding everywhere. The structure of high-precision injection mold mostly adopts inlay or full assembly structure, which requires the processing accuracy and interchangeability of mold parts to be greatly improved.
對于注塑件而言,大多是與其它零部件配套組成完整的產(chǎn)品,而且在很多的情況下都是在其它部件已經(jīng)完成,急切等待注塑件的配套上市。因?yàn)閷χ破返男螤罨虺叽缇纫蠛芨?,加之由于樹脂材料的特性各異,模具制造完成后,還需要反復(fù)地試模與修正,使開發(fā)和交貨的時(shí)間非常緊張。
For injection molded parts, most of them form complete products with other parts, and in many cases, other parts have been completed, eagerly waiting for the supporting products of injection molded parts to be listed. Because of the high requirements for the shape or dimensional accuracy of products, and the different characteristics of resin materials, after the completion of mold manufacturing, it is necessary to repeatedly try and correct the mold, which makes the development and delivery time very tight.
山東模具制造廠家提醒您,模具制造不是終目的,而是由用戶提出終制品設(shè)計(jì),模具制造廠家根據(jù)用戶的要求,設(shè)計(jì)制造模具而且在大多數(shù)情況下,制品的注射生產(chǎn)也在別的廠家。這樣就造成了產(chǎn)品的設(shè)計(jì)、模具設(shè)計(jì)制造和制品的生產(chǎn)異地進(jìn)行的情況。
Shandong mold manufacturers remind you that mold manufacturing is not the end goal, but the end product design proposed by the user. Mold manufacturers design and manufacture molds according to the requirements of users. In most cases, the injection production of products is also in other manufacturers. In this way, the product design, mold design and manufacturing and product production are carried out in different places.
模具生產(chǎn)批量小,一般屬于單件的生產(chǎn),但是模具需要很多的標(biāo)準(zhǔn)件,大到模架,小到頂針,這些不能也不可能只由一個(gè)廠家單獨(dú)完成,且制造工藝復(fù)雜,普通設(shè)備和數(shù)控設(shè)備使用不均衡。
The production batch of molds is small, which generally belongs to single piece production. However, molds need many standard parts, ranging from mold base to thimble. These can not and cannot be completed by only one manufacturer. Moreover, the manufacturing process is complex, and the use of ordinary equipment and CNC equipment is uneven.
The above is the relevant content about the problem shared for you today. I hope it can help you. If you want to know more, you can contact us by phone or follow our website http://m.samsungstarex.com.cn 。